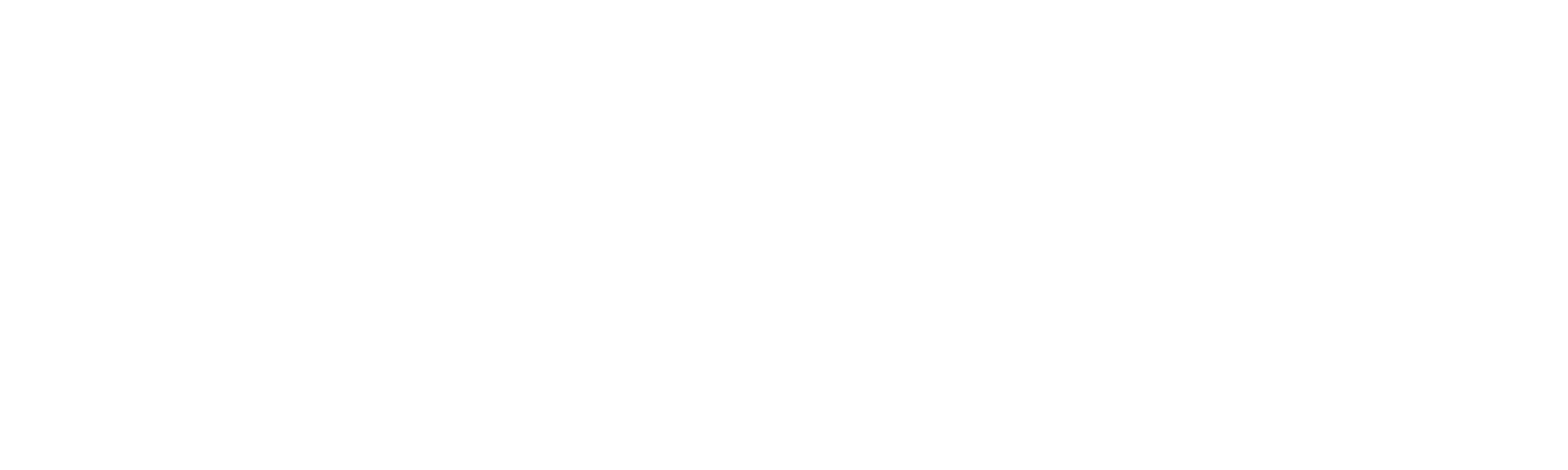
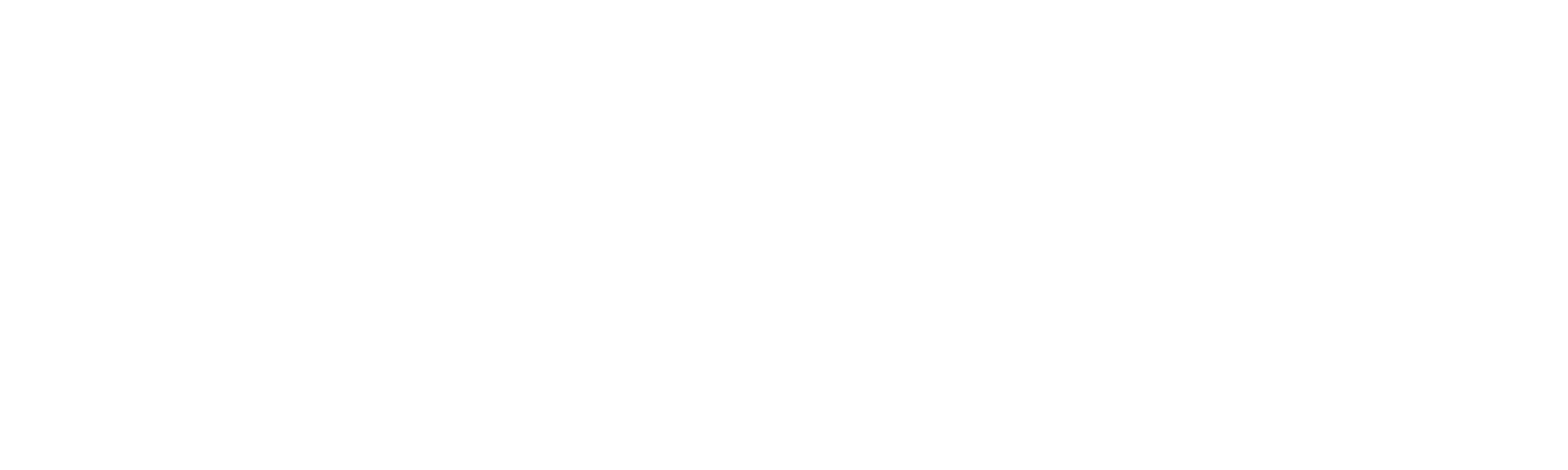
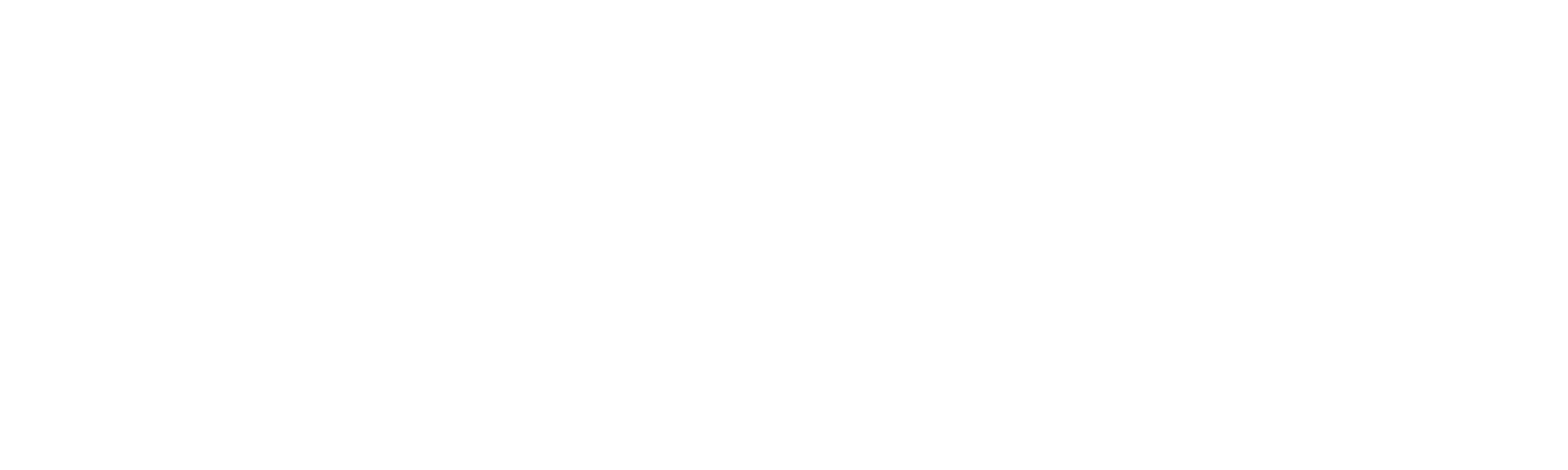
Our Company
Our company was founded on the idea of creating practical and effective solutions for companies facing high noise and tough communication challenges. We have enjoyed over 25 years success by building strong relationships with our customers. Practical solutions can only be shaped through listening to our clients' needs to fully understand your specific situation, concerns, and objectives. Equally important is CavCom’s commitment to developing solutions that are embraced by the end user, your employee. We design products that are simple to use, are comfortable for long term use, and address personal safety to enhance successful implementation and consistent use.
Proudly Women-Owned and SBA-Certified
We are a proud Women-Owned Business and a member of the Small Business Association (SBA). As a certified HubZone company, we are committed to fostering economic growth in underrepresented communities while delivering exceptional service and quality to our clients. Our team combines passion, expertise, and a dedication to excellence, ensuring that we not only meet but exceed expectations in every project we undertake.
Innovative Technology
Since 1997, CavCom has been revolutionizing hearing protection and two-way communication with game-changing innovations. From our award-winning Talk Through Your Ears® technology to RadioGear®, TeamTalk™, EarzON® custom hearing protection and much more, CavCom‘s commitment to developing innovative technology helps keep your workforce safer and more productive. We are also proud to offer a complete line of two-way radios, PoC systems, and full-duplex communication for our customers.
Our solutions-approach integrates extensive experience, proprietary cutting-edge technology, and dedicated customer support to address virtually any challenging communication situation. Our passion is improving worker safety, productivity, and preservation of hearing through partnership with our customers. Simply put, your success is our top priority.
Breaking Barriers: Beth Orton, the Woman Owner Driving Success at CavCom
Beth Orton is the President and Owner of CavCom, a thriving women-owned business she’s been part of since 2006. Over the years, Beth has worked across every corner of the company—from finance and operations to sales, marketing, and management. Her passion for the business and hands-on leadership style have been key to CavCom’s success, and in 2023, she purchased CavCom, guiding the company to new heights.
Beth holds dual degrees in Economics and Business Management from the University of St. Thomas in Minnesota. Her educational background, combined with years of experience in the trenches, has shaped her thoughtful, results-driven approach to leadership.
When she’s not running CavCom, Beth is deeply involved in community service and volunteer work, always seeking ways to give back and make a positive impact. Her leadership reflects a balance of business acumen, compassion, and a commitment to making a difference—both in her industry and in the world around her.
Customer Service is our priority
CavCom is a true partner by working directly with you to solve your unique challenges. We expertly tailor solutions to your needs by collaborating with safety & health personnel, management, and end-users. Warranty, repairs, and customer service are also handled directly to ensure optimum customer satisfaction. We are committed to improving performance, safety, and employee participation in your hearing conservation and communication programs, one success at a time.